Die casting is a common manufacturing process that produces metal objects with great precision and a smooth surface finish. It entails pouring molten metal into a mould chamber under pressure, where it solidifies to the desired shape. There are two types of die casting: low pressure and high pressure. Each approach has distinct advantages and is appropriate for various purposes.
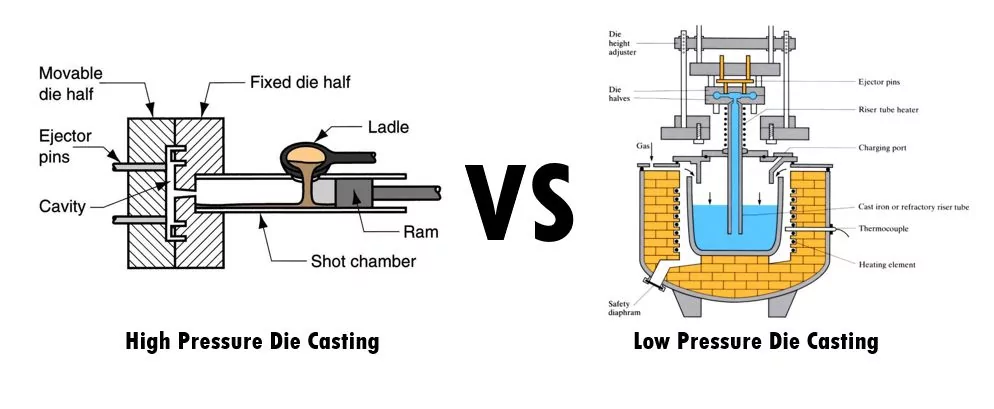
In this guide, we will compare low-pressure die casting and high-pressure die casting and discuss its advantages and disadvantages.
Low Pressure Die Casting
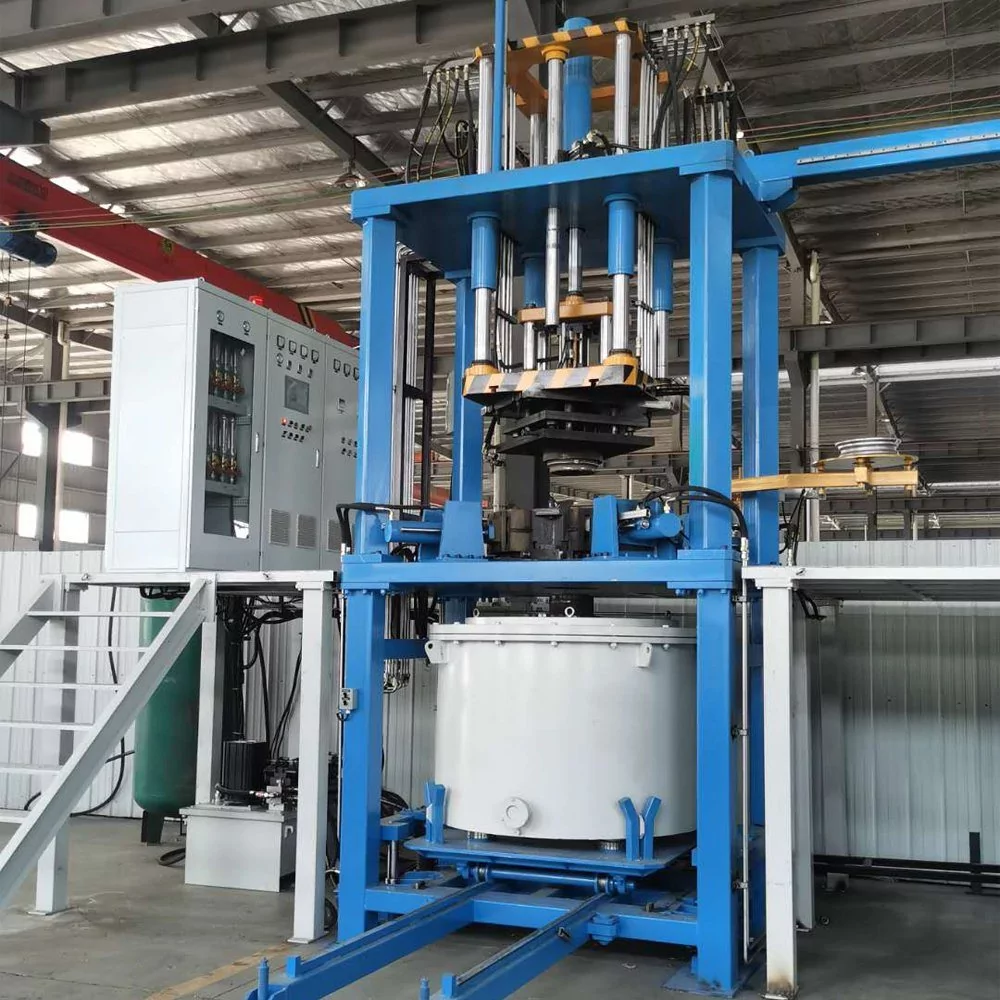
Melted metal is poured into a die-cast mould at low pressure in LPDC. The fact that the die cavity is continuously filled during the solidification or shrinking phase contributes to its great accuracy, which indicates that it makes up for the volume drop. Additional characteristics include improved uniformity of the molten metal from top to bottom and a decrease in porosity and oxide development.
Features
Low pressure die casting (LPDC) is a specialized process characterized by the use of low pressure, typically ranging from 0.7 to 1.5 bar, to force molten metal into the mold cavity. This method is designed to produce high-quality metal parts with excellent mechanical properties and intricate geometries. Here are some key features of low pressure die casting:
- Low Pressure Application: The process uses relatively low pressure to fill the mold, which reduces the risk of turbulence and minimizes the formation of gas porosity in the final product. This results in parts with superior structural integrity and fewer defects.
- Slow Fill Rate: The slow and controlled fill rate of molten metal helps in maintaining a steady and uniform flow, which is essential for achieving fine details and reducing the likelihood of cold shuts and misruns.
- Gravity-Assisted Filling: In LPDC, the mold is typically positioned above the molten metal reservoir, allowing gravity to assist in the filling process. This helps achieve better mold filling and reduces metal wastage.
- Reusable Molds: The process employs reusable metal molds (dies), which offer good thermal conductivity, leading to faster cooling and solidification of the metal. This improves cycle times and overall production efficiency.
- Reduced Turbulence: The controlled pressure and slower filling rate significantly reduce turbulence during the casting process. This minimizes the risk of trapped air and inclusions, leading to a higher-quality surface finish.
- Versatile Applications: LPDC is suitable for producing a wide range of components, including automotive parts (e.g., wheels, engine blocks), aerospace components, and structural parts for various industries. It is particularly well-suited for producing large and complex parts with tight dimensional tolerances.
Pros
The advantages of Low Pressure Die Casting are:
- Excellent Formability
Low-pressure filling enhances the liquid metal’s fluidity, resulting in good formability. Castings produced with this method have a smooth surface and distinct form. Due to its excellent formability, the method is generally perfect for creating cast parts with intricate geometries.
- High Pure Castings
There is very little to no slag present in the castings, which makes them extremely pure. The casting machine’s configuration is the reason for the low slag level. On the surface of molten metals, slags are typically seen. Still, the liquid metal driven into the cavity does not contain slags since the riser tubes descend into the holding furnace. Thus, the exceptionally pure casting. Slag has a minimal probability of getting into the mould because this is a low pressure procedure.
Due to the stable filling process, the technique also prevents the molten metal from oxidising. When the molten metal is stable, its tumbling, hitting, and splashing are lessened or eliminated. As a result, no oxidation slags form, which might compromise the castings’ quality.
- Crystallization
The casting is able to crystallise and create a compact structure because it solidifies under pressure. As a result, castings created using this method are sturdy and appropriate for items that need to have high strength values.
- Increased Accuracy
The method produces extremely accurate parts because the solidification process is conducted at a low pressure. Consequently, the die cavity is continuously filled to compensate for the volume that shrinks as the molten metal solidifies. Because of its great precision, it is the most accurate process for creating axially symmetrical objects, like wheels.
Cons
Here are some of the disadvantages of Low Pressure Die Casting:
- Unsuitable for Producing Parts with Thin Walls
Castings made with this method can have walls as thin as 3 mm at the very least. As such, high-pressure die casting is a better option for producing thin-walled parts than this method.
- Eroded Metal Part
When equipment metal comes into contact with molten metal, eroded aluminum casting form may result. This may result in high maintenance expenses, particularly in large manufacturing systems. Moreover, the liquid metal may absorb the components of the equipment metal portion, which could impair performance.
- Reduced Casting Cycle
One drawback is that because of the low pressure, its cycle is slower. As a result, few parts can be manufactured, and they are expensive.
High Pressure Die Casting
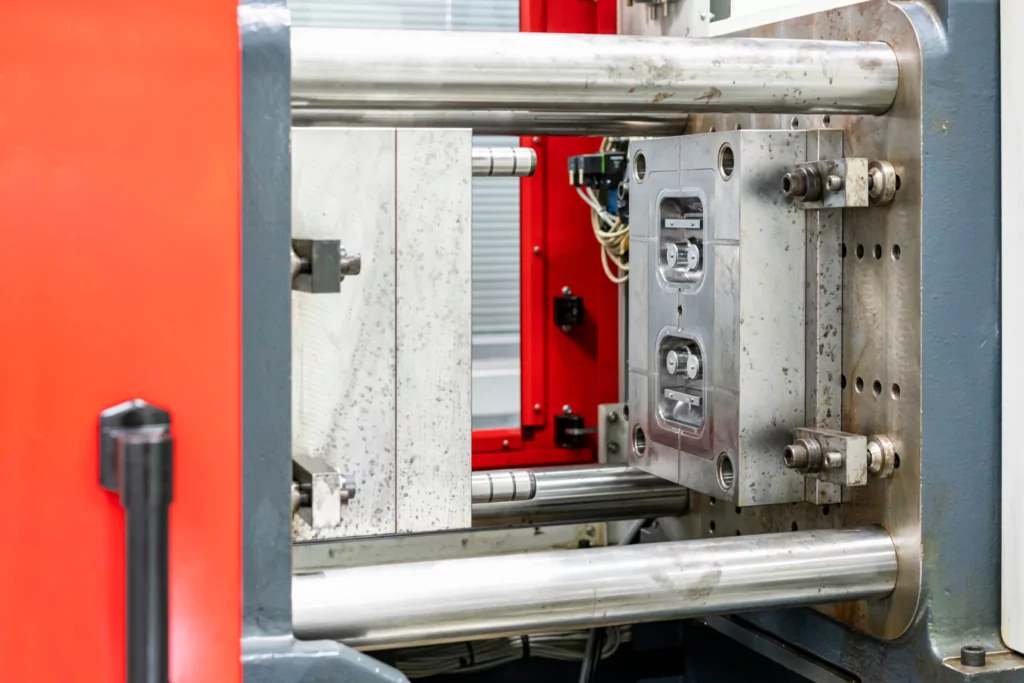
High-pressure die casting involves pouring the metal liquid into the pressure chamber, quickly filling the mould cavity, allowing the metal to crystallise and solidify under high pressure, and then creating solid cast aluminum pieces. High-pressure die casting is the best method for producing large quantities of aluminum parts with excellent dimensional precision and a smooth surface finish while requiring little machining. This is a good way to make aluminum castings that are high in strength. Furthermore, high pressure die casting offers the possibility of producing thinner wall sections than either gravity casting or low pressure die casting.
Features
High pressure die casting (HPDC) is a highly efficient and widely used manufacturing process known for its ability to give complex and high-precision metal parts at high production rates. Here are some key features of high pressure die casting:
- High Injection Pressure: HPDC involves injecting molten metal into the mold cavity at very high pressures, typically ranging from 700 to 2500 bar. This high pressure ensures that the molten metal fills the mold quickly and completely, even in the case of thin-walled or complex geometries.
- Rapid Cycle Times: Due to the high pressure and fast injection speeds, HPDC allows for very rapid cycle times, making it ideal for high-volume production. This efficiency can significantly reduce manufacturing costs and increase productivity.
- Precision and Accuracy: The high pressure used in HPDC ensures that the metal conforms precisely to the mold’s dimensions, resulting in parts with high dimensional accuracy and tight tolerances. This makes HPDC suitable for producing intricate components with fine details.
- Thin Wall Sections: The ability to inject metal at high pressures enables the production of parts with very thin walls, which is not easily achievable with other casting methods. This is particularly advantageous for lightweight applications in industries such as automotive and aerospace.
- Reusable Metal Molds: Similar to LPDC, HPDC uses reusable metal molds (dies) made of high-strength steel. These molds can withstand the high temperature and pressures involved in the process, contributing to the method’s cost-effectiveness.
- Surface Finish: HPDC typically produces parts with excellent surface finish and minimal post-processing requirements. The high pressure ensures a smooth, dense surface, decreasing the need for extra machining or finishing.
- Alloy Compatibility: HPDC is compatible with a wide range of metal alloys, including aluminum, zinc, magnesium, and copper. This versatility allows manufacturers to select the best material for their specific application needs, balancing factors such as strength, weight, and cost.
Pros
Below are the advantages of the high pressure die casting process:
- Smooth Surface Finish
The smooth surfaces of HPDC components make them perfect for coatings or other finishing touches. As a result, fewer secondary CNC machining procedures are required, saving both money and time. Additionally, it enhances the final product’s aesthetic appeal, which is especially advantageous for consumer items.
- Thin-Walled Components
This process’s high pressure enables the casting of components with walls as thin as 1 mm. This attribute helps produce lightweight but strong and durable parts, which is helpful for industries such as electronics, automotive, and aerospace.
- Production is Cost Effective, and Swift
HPDC is a productive procedure. Because it can quickly create large numbers of parts, it is frequently the most economical choice for high-volume production runs. Over time, the speed and accuracy of casting cycles ensure lower cost per unit, which also guarantees decreased waste and higher efficiency.
CONS
Below are the disadvantages of using the high-pressure die casting process:
- High Start-up Costs
HPDC has considerable upfront expenditures, especially for tooling and setup. These expenses can be prohibitive for small-scale manufacturing or prototyping. However, in high-volume production runs, these expenses are frequently offset over time by decreased unit costs.
- Porosity Issues
One typical issue with HPDC is porosity, which is the production of microscopic holes or gaps in the cast part as a result of trapped gas. Porosity can damage the cast’s mechanical characteristics, shorten its longevity, and degrade its beauty. While proper design and process control can reduce this problem, it cannot be totally eradicated.
- Limited Heat Treatment
The porosity in HPDC further limits the capacity to thoroughly heat-treat components after casting. Heat treatment, which is frequently used to increase the strength and durability of metal parts, may be less effective due to the presence of porous areas.
Low Pressure vs High Pressure Die Casting
Here is a table showing a contrast between low pressure and high pressure die casting:
Features | Low pressure die casting | High pressure die casting |
Pressure Applied | Low (0.7 to 1.5 bar) | High (700 to 2500 bar) |
Fill Rate | Slow and controlled | Fast |
Turbulence | Low, reducing gas porosity and inclusions | High, requiring careful management to avoid defects |
Cycle Time | Moderate | Rapid |
Dimensional Accuracy | High, suitable for intricate geometries | Very high, ideal for complex and detailed parts |
Wall Thickness | Thicker sections | Capable of producing thin-walled parts |
Surface Finish | Good, it may require some post-processing | Excellent, often minimal post-processing needed |
Material Compatibility | Various alloys (aluminum, magnesium, copper-based alloys) | Wide range of alloys (aluminum, zinc, magnesium, copper) |
Production Volume | Suitable for medium to high production volumes | Highly cost-effective for large-scale production |
Common Applications | Automotive parts (wheels, engine blocks), aerospace components, structural parts | Automotive components, electronics, consumer goods, and more |
Conclusion
Choosing between low pressure die casting (LPDC) and high pressure die casting (HPDC) depends on your specific manufacturing needs and production goals. Low Pressure Die Casting (LPDC) is ideal for parts needing excellent mechanical properties and intricate geometries. However, high Pressure Die Casting (HPDC) excels in high-volume production with rapid cycle times. Understanding these diferences will help you choose the process that aligns best with your production requirements and application demands.
Great, Together